Navigating the Nexus: How the Food Traceability Final Rule and the New Era Initiative Reshape CPG Industry Compliance

The food industry is experiencing a transformative shift as regulatory bodies and technological advancements converge to create a more transparent food supply chain. The Food Safety Modernization Act (FSMA), Food Traceability Final Rule, and the New Era of Smarter Food Safety initiative are working in tandem to reshape the landscape for Consumer Packaged Goods (CPG) brands. These pivotal regulatory frameworks each play a critical role in advancing how brands manage food safety, ushering in an era of heightened compliance, innovative technology adoption, and increased consumer trust.
Food Safety Regulations For CPG Brands
The Food Safety Modernization Act (FSMA) indicates a fundamental shift in food safety regulation, pivoting the focus from merely responding to foodborne illnesses to actively preventing them. This groundbreaking legislation has significantly expanded the FDA's authority over food safety, ushering in a new era of stringent standards and proactive measures throughout the entire food supply chain.
One of the critical components of FSMA is the Food Traceability Final Rule, designed to improve the traceability and tracking of food products. This rule mandates comprehensive record-keeping and traceability requirements, particularly for foods identified as high-risk. The aim is to accelerate response times during outbreaks and ensure broad compliance across the industry, facilitating quicker containment and resolution of potential public health threats.
Building on the foundation set by FSMA and the Traceability Final Rule, the New Era of Smarter Food Safety initiative represents a strategic integration of modern technological innovations to enhance food safety practices further. By leveraging advanced tools such as Artificial Intelligence (AI), blockchain, and the Internet of Things (IoT), this initiative seeks to transform the food safety landscape into one that is more digital, traceable, and inherently safer.
This new regulatory environment fosters a collaborative approach between the governing agencies and CPG brands to improve food safety outcomes by sharing insights, data, and best practices. As food supply chains become increasingly global, these measures drive innovation and transparency to ensure that food safety regulations keep pace with technological advancements and the complexities of a global food market.
Food Traceability Final Rule Requirements
The FDA's Food Traceability Final Rule requires specific KDEs to be documented at designated points in the supply chain. These elements are crucial for ensuring traceability and rapidly identifying potential contaminations in the event of a food safety issue.
Key Data Elements (KDEs)
KDEs vary depending on the type of CTE but generally include the following types of information:
- Origin and Destination Information:
Source: Information about where the food item was grown, harvested, manufactured, or processed before arriving at a specific location.
Receiver: Information about the next point in the supply chain where the food item will be sent, including the name and address of the entity receiving the product.
- Date and Time:
Detailed records of when a product was received, transformed, or shipped help establish a timeline for tracking its movement through the supply chain.
- Quantity and Description:
The amount and detailed description of the food product being transferred or processed. This may include the size, weight, volume, and specific identifiers like lot or batch numbers.
- Lot or Batch Number:
If applicable, the specific lot or batch number associated with the food product to facilitate precise tracking and identification in case of a recall or investigation.
- Purpose of Transaction:
A description of why the transaction is taking place (e.g., shipping, processing, transformation) helps understand the product flow.
Each CTE requires accurate documentation of KDEs to ensure that the traceability system can function effectively, enabling rapid responses to food safety issues and ensuring compliance with regulatory requirements.
Critical Tracking Events (CTEs)
CTEs are specific activities or points in the supply chain where the recording of KDEs is required to ensure traceability.
Harvesting: Capturing details when the product is harvested.
Receiving: When a product is received at a processing plant, distribution center, or retail outlet.
Transforming: Any process that changes the state or nature of the product (e.g., slicing, cooking, packaging).
Shipping: When products are sent from one location to another.
Expanded Roles in Regulating CPG Brands
The expanded authority set forth by these frameworks actively ensures that food producers adhere to preemptively identified safety measures rather than merely reacting to incidents. This includes routine inspections, compliance checks, and the ability to mandate recalls if necessary, significantly reducing the risk of widespread foodborne diseases. These initiatives bridge traditional regulatory approaches and modern technological capabilities, encouraging CPG brands to adopt cutting-edge solutions that provide real-time data and insights into the food supply chain.
Challenges for CPG Teams
CPG brands face several challenges in adapting to these regulations. Integrating new technologies to meet traceability requirements often requires substantial investment in systems and training. Maintaining the balance between operational efficiency and regulatory compliance also necessitates ongoing adjustments to business practices and supply chain operations.
The complexity of these regulations also requires CPG brands to be continually updated on the legal requirements, which vary significantly depending on the product and market. As such, these frameworks are pushing companies to embrace cutting-edge technologies to meet stringent food safety standards set by the Food Traceability Final Rule while also building consumer confidence. Brands must cultivate a culture of compliance and safety, embedding these principles into every level of their operations.
Technological Empowerment: The Critical Role of Retail Execution Software in CPG Success
The rapid development of retail execution software (RES) is playing a transformative role in enabling CPG brands to exceed regulatory requirements by providing advanced analytics, real-time data monitoring, and seamless record keeping.
Enhanced Data Collection and Management
Comprehensive Record-Keeping: RES solutions can automate the capture and storage of detailed data at points in the supply chain. This includes critical tracking events (CTEs) and key data elements (KDEs) as required by the Food Traceability Final Rule. This automated data entry minimizes human error and ensures all necessary information is accurately recorded and easily accessible.
Advanced Forecasting: One of the standout features of RES is its ability to analyze buying patterns and predict future demand based on historical data. This analysis can inform recommended orders, particularly focusing on the timing of when products are likely to expire. Such features ensure that inventory levels are optimally managed, reducing waste and improving the efficiency of the supply chain.
Integration with Existing Systems: Today’s advanced RES solutions integrate with ERP (Enterprise Resource Planning) and SCM (Supply Chain Management) systems to pull and consolidate data from various sources. This integration ensures the traceability data is comprehensive and up-to-date, facilitating quick access to complete product histories.
Real-Time Traceability and Visibility
GPS and IoT Integration: By incorporating GPS tracking and IoT sensors, some RES solutions can monitor shelf conditions and product locations in real-time throughout the supply chain. This capability ensures products are stored and transported safely, reducing compliance risks. Moreover, integrating IoT devices with RES optimizes supply chain logistics, from automated reordering to dynamic route planning, reducing transportation time and operational costs.
Enhanced Transparency: RES tools can give stakeholders a transparent view of the operations, from production to point of sale. This transparency is critical not only for internal audits and regulatory compliance but also for building trust with consumers and partners.
Rapid Response to Compliance Issues
Automated Alerts: RES solutions can be configured to send automatic alerts when potential compliance issues are detected, such as deviations from required storage conditions or mishandling of products. This allows CPG teams to take immediate corrective action and prevent minor issues from becoming major compliance violations.
Supply Chain Collaboration: RES facilitates better collaboration across the supply chain, aiding in recall management. By enabling seamless data sharing between manufacturers, distributors, and stores, these systems ensure that all stakeholders can access consistent and accurate information. This collaboration is crucial for synchronizing operations and ensuring that all parties are aligned with compliance and safety standards.
Reporting and Analytics
Compliance Reporting: RES solutions can generate reports that detail product traceability and adherence to safety standards. These reports are essential for regulatory bodies' internal reviews, audits, and inspections.
Predictive Analytics: Leveraging AI and machine learning, RES can analyze historical data to predict potential compliance issues, allowing CPG teams to proactively address them before they arise.
Looking Ahead
The synergy between the FSMA, the Food Traceability Final Rule, and the New Era initiative creates a robust framework that enables brands to meet current regulatory requirements and anticipate and adapt to future changes within the industry. This integration of policy, practice, and technology ushers in a new era of food safety—a transformative period where transparency, efficiency, and consumer trust merge to forge a safer, more dependable food supply chain.
As CPG brands maneuver through these evolving regulations, embracing technological advancements is the key to their future success. By investing in sophisticated traceability systems and building strategic partnerships, CPG leaders are well-equipped to tackle upcoming challenges, seize new opportunities, and reinforce their reputation as pioneers in food safety and consumer confidence.
Eager to master the complexities of the Food Traceability Final Rule and its impact on your merchandising team? Download Movista's "Beyond Compliance: Understanding the Impact of Food Traceability Final Rule on Merchandising Teams" whitepaper now!
This guide is essential for any CPG brand looking to navigate the nuances of current regulations and leverage them for strategic advantage. Dive deep into expert insights and practical strategies that will not only ensure compliance but also enhance your operations and consumer trust. Get your free copy today and stay ahead in the evolving landscape of food safety and transparency.
featured content
featured content
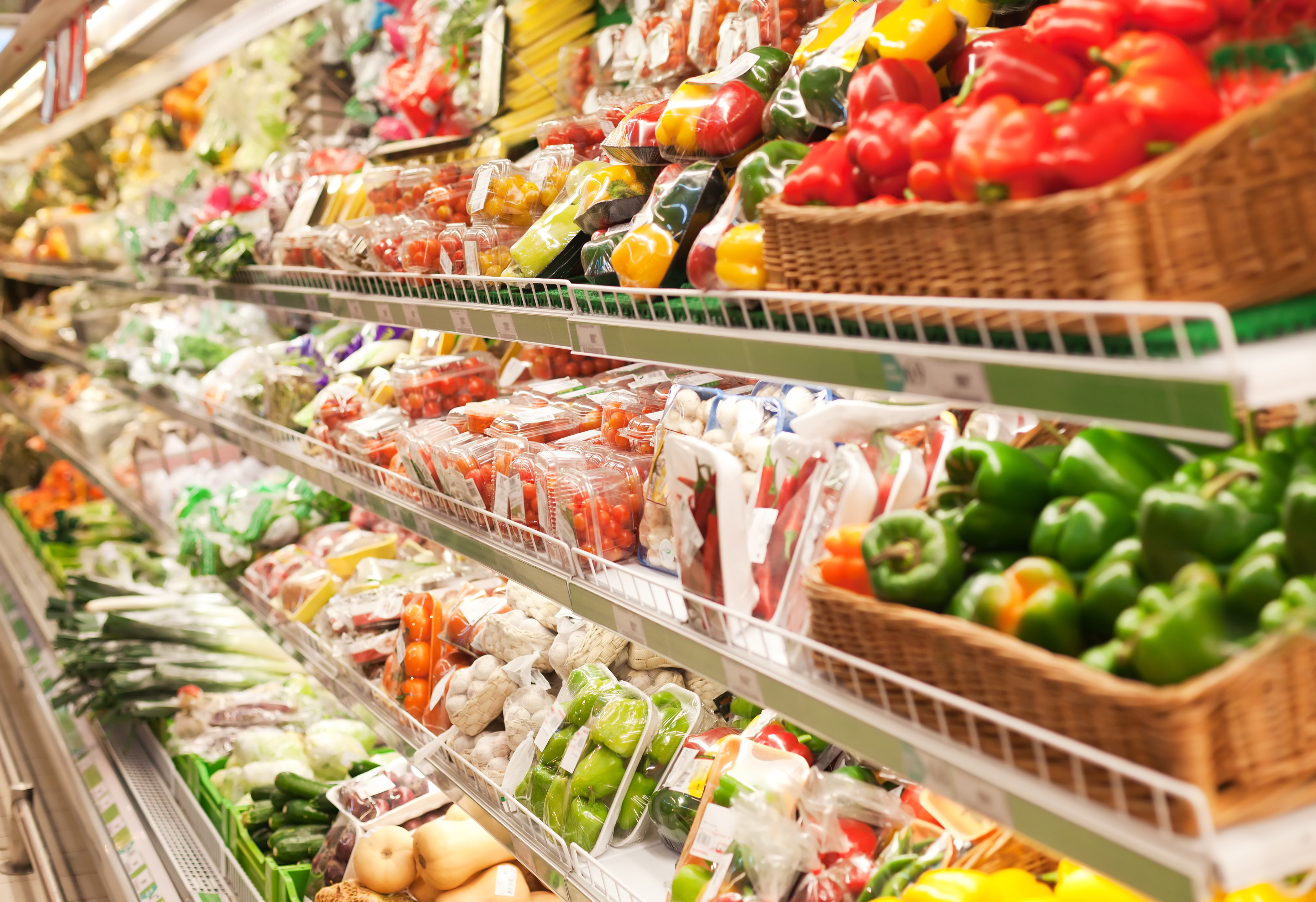
Fresher Inventory Management through Unified Planning and Execution
The key to improving fresh food inventory management is to unify the teams & technology of central planning & store execution. Learn why in this thought leadership blog between Movista and RELEX Solutions.